Как настройка инструмента вне станка до 80% сокращает простои станков и вспомогательное время.
Решения Haimer являются на данный момент одними из самых выгодных и быстроокупаемых инвестиций для российских предприятий.
Что изменилось, когда подразделение Microset стало частью объединения Haimer Group?
Процесс интеграции происходит с энтузиазмом и довольно оперативно, появилось множество вещей и идей, которые вместе реализуются для того, чтобы увеличить производительность и эффективность собственного производства – за последние три года был увеличен выпуск продукции, выпуск реализуемых приборов, и в целом, сделан большой шаг к цифровизации и к дальнейшей цифровой интеграции оборудования как в свое производство, так и в производство клиентов.
Первая задача, которая была решена – интеграция пресеттеров, создание участков технологической подготовки на основном производстве Haimer. Данный процесс был реализован за короткий промежуток времени, без единой аварии, в результате чего не было получено ни одного брака по причине неправильной настройки инструмента и операторы получили более удобную производительную систему для обслуживания всех имеющихся станков.
После того, как была сделана единая база всех станков, сотрудники получили возможность выполнять все задачи централизовано и обеспечивать свой спектр оборудования. Это дало как оптимизацию так и производительность самим приборам.
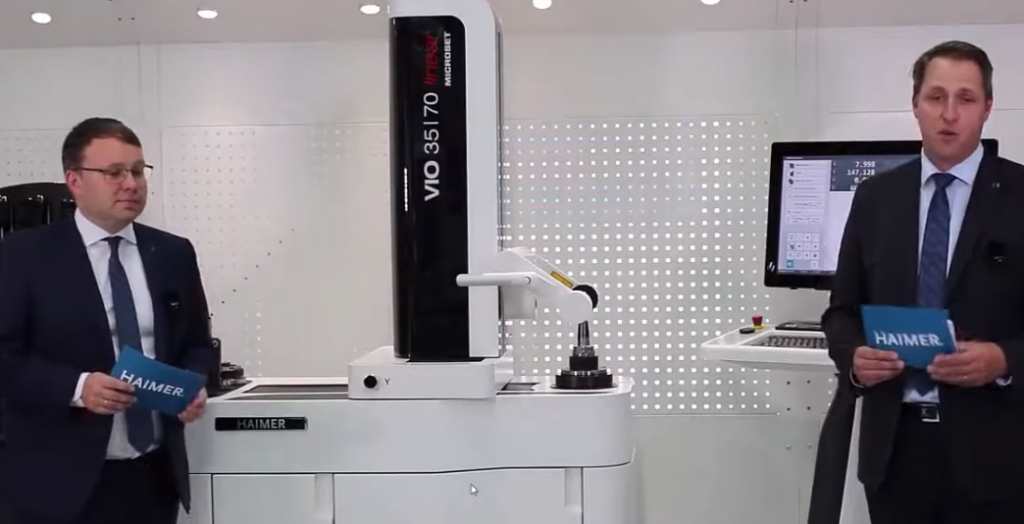
Более того, в процессе данной работы Microset смог оптимизировать и написать постпроцессоры для всех главных игроков на рынке оборудования и выработать решения выполнения разных задач. Теперь любые станки могут подключать и получать правильную автоматизированную систему для предварительной настройки.
Сегодня мы наглядно увидим множество примеров интеграции и вариантов использования пресеттеров. Главная наша цель — показать и доказать, что предприятия, использующие привязку инструмента вручную, без использования специальных устройств, теряют множество средств и времени, что отражается на работе предприятия в целом.
Сравнение ручного способа привязки инструмента и настройки на пресеттере.
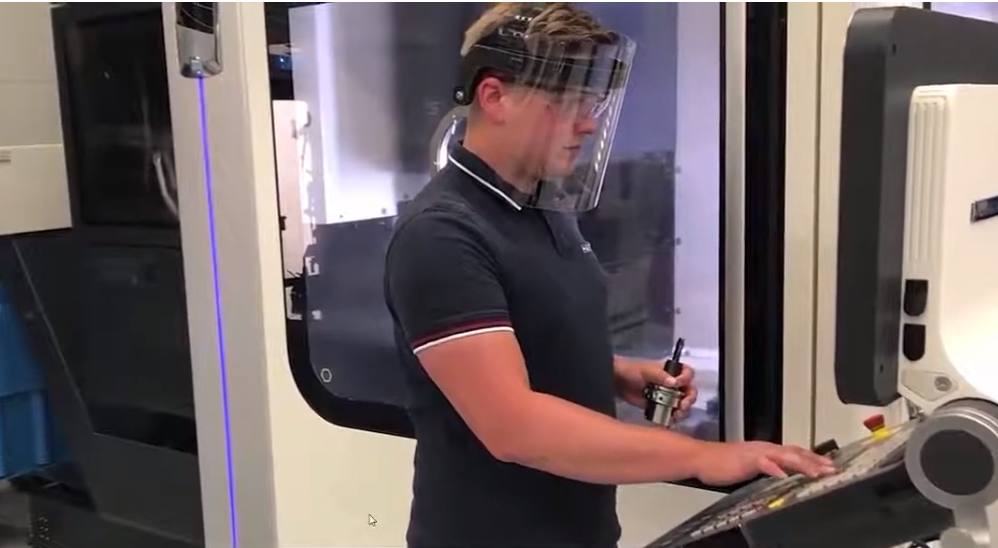
Не сложно заметить, что сам процесс ручной настройки инструмента довольно трудоемкий, и требует высокой точности и осторожности – только на получение нулевого параметра по оси Z ушло больше 2-х минут, причем все это время станок не обрабатывает и не снимает стружку. Если мы будем вести отчет времени с момента, когда оператор предварительно измеряет приблизительные диаметры и длину до полного завершения обработки, то весь процесс занял чуть более 4 минут.
В общем случае, говоря про серийное производство, мы имеем примерно 10% увеличения производительности каждого машинного центра, поскольку каждый инструмент, который измеряется без специального прибора требует примерно 3 минуты времени и это мы говорим про простой инструмент. Если же мы говорим про более усложненную систему, то это время, соответственно, увеличится еще больше.
Теперь посмотрим, как аналогичный процесс будет выполняться при помощи пресеттера из серии VIO.
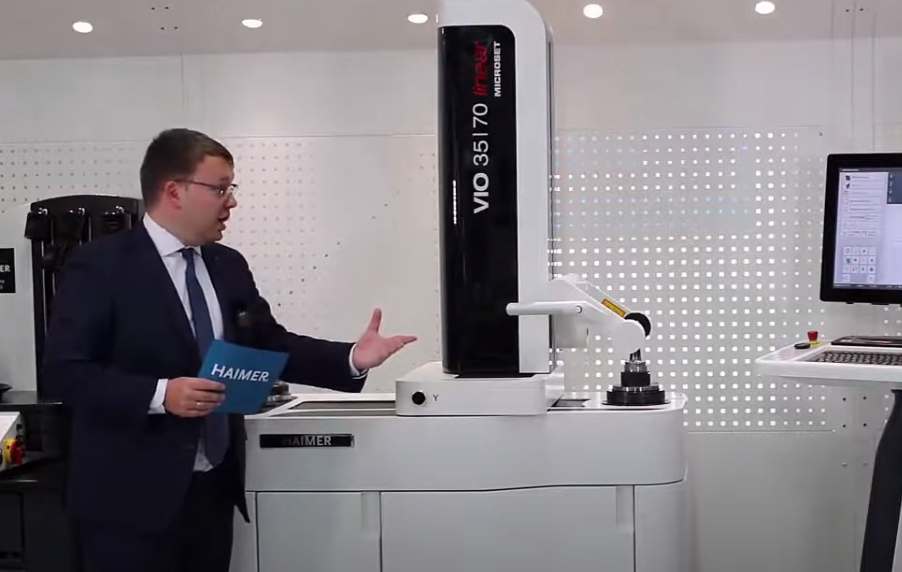
Благодаря функции «Sigma», которая предполагает вращение на 360 градусов и измеряет каждую режущую кромку, а также измерение реальных параметров и биение данного инструмента, процесс занял не более 30 секунд. Далее мы можем загрузить получившиеся данные на постпроцессор или на этикетку. При печати на ней, помимо диаметра и длины инструмента, мы можем измерять также углы, радиус, радиус режущей кромки, если это требуется.
Настройка инструмента с помощью станка с лазерной измерительной системой и с помощью пресеттера и постпроцессора
Ошибочное мнение заключается в том, что при наличии лазерной измерительной системы, которая идет как отдельная, компании могут думать, что приобретать пресеттер нет необходимости. В таком случае, теряется машинное время, и такая установка требует дополнительных финансовых вложений, поскольку если у вас имеется несколько станков, то необходимо устанавливать такую систему на каждый из них.
Естественно, для некоторых сверхточных операций , когда требуется измерить инструмент с учетом температурной компенсации нагрева деталей инструмента, применение такой опции уместно, в остальных же случаях в этом нет необходимости
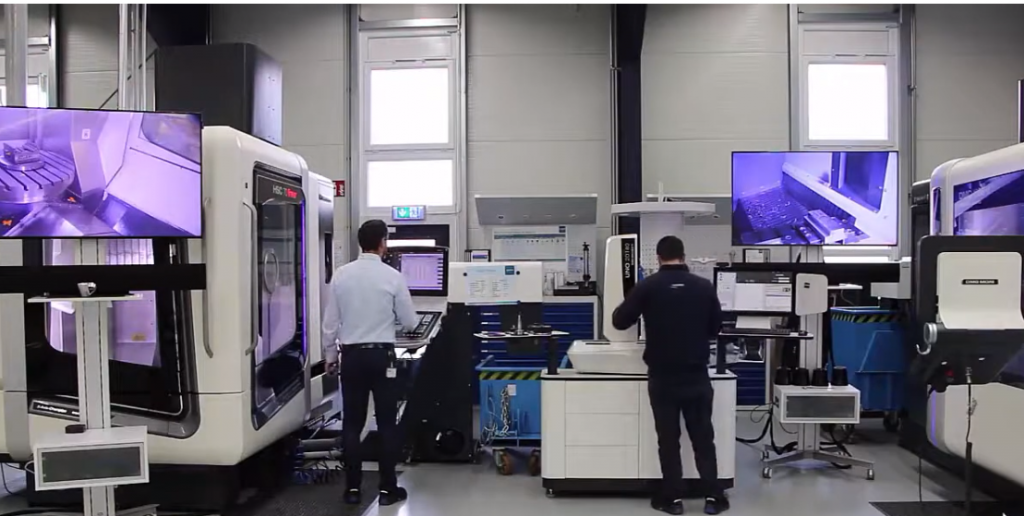
Слева обрабатывающий центр с лазерной измерительной системой проводит настройку инструмента, на правой стороне оператор измеряет инструмент с помощью пресеттера UNO Premium и передает данные инструмента на постпроцессор. Поскольку данные уже сразу загружены и перенесены в систему, уже через пару секунд начинается обработка детали, принося деньги владельцу.
Таблица окупаемости
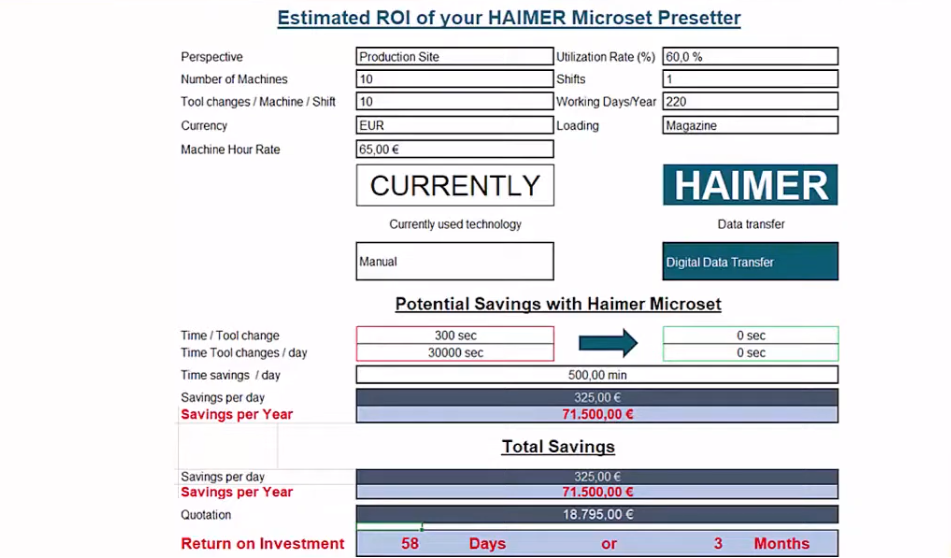
Перед нами таблица окупаемости для пресеттера, средний случай. При наличии 10 машин на производстве, которые работают в одну смену, стоимость часа составляет примерно 65$ и при коэффициенте использования 60%, получается 220 дней работы в году. При таких условиях мы получим окупаемость данного вложения всего лишь через два-три месяца. Таким образом, приобретение пресеттера– одно из лучших вложений, существующих на рынке вспомогательного оборудования для обрабатывающих центров.
Отдельное внимание хочется уделить не просто измерению, а именно настройке и выставлению инструмента. Выставление регулируемого инструмента, его нужного размера и получение первой годной детали – процесс очень важный, т.к. часто скрывает большие временные затраты, а соответственно- потерю денег. Улучшение этого процесса даст большой экономический эффект. При этом процессе пресеттер позволяет контролировать биение и выполняет функцию контроля качества и контроля технологической цепочки.
Сравнение времени настройки расточной системы. Стандартный способ и настройка с пресеттером.
Теперь сравним время настройки расточной системы с помощью стандартного метода , когда мы будем настраивать расточную голову с помощью калибра на проход и не проход, а далее выставлять аналогичную расточную систему и проверять результат при помощи пресеттера.
Стандартный способ
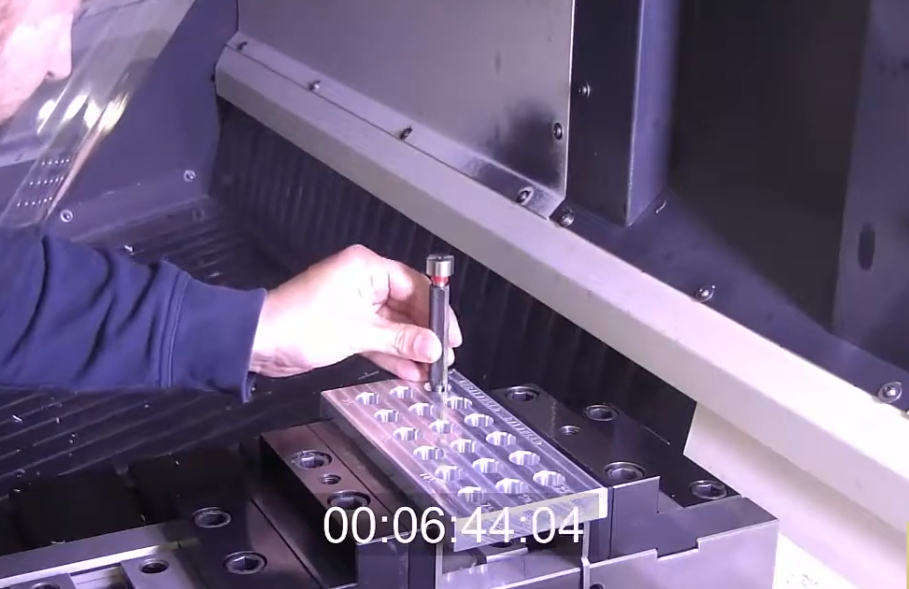
При помощи рисок на расточной системе оператор выставляет отверстие 18 мм с небольшим запасом, заносит изначальные параметры в систему, ставит на станок. В первой операции на небольшую длину делается пробное отверстие на 5 мм, далее мы измеряем данное отверстие с помощью проходного и не проходного калибров. После этого при помощи микрометрической настройки корректируем размер. Далее проделываются такие же действия до того момента, пока калибр не будет проходить в отверстие, только тогда процесс можно считать завершенным. На все это ушло примерно 7 минут.
Если же таких отверстий нет, можно использовать метод балансировки кольцами. Кольца одеваются на цилиндрическую поверхность оправки , фиксируются винтами, и машина подсказывает, какое кольцо под каким углом необходимо повернуть. У колец есть своя величины дисбаланса, и все необходимые исходные данные вносятся в машину.
При помощи пресеттера
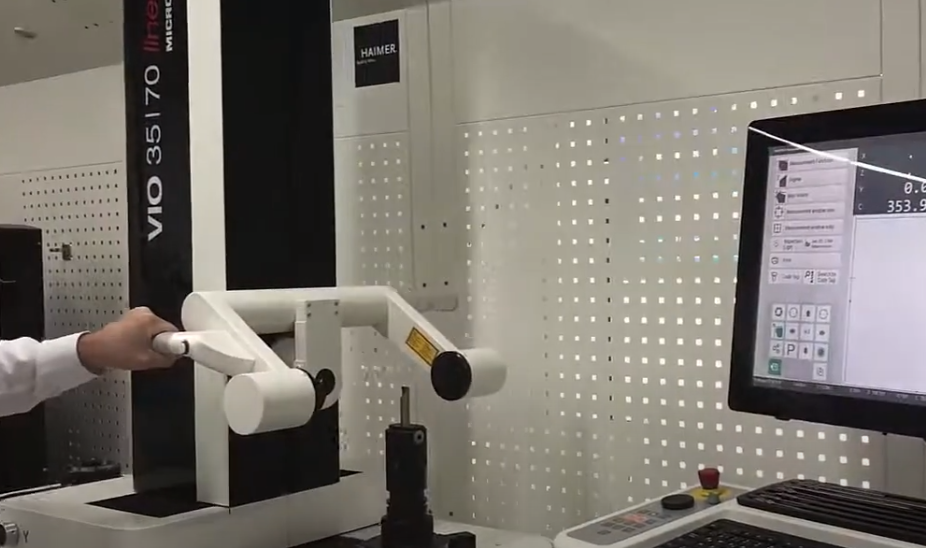
Проведем такую же операцию на пресеттере VIO. Демонстрация начинается с функции измерения «Measure by touch» при помощью касания. При нажатии на датчик касания, машина автоматически передвигается в парковочную позицию. Когда оператор берется за ручку, данный датчик автоматически отключает тормоза на приводах, позволяя передвигать машину в нужную позицию, а лазерный индикатор помогает найти режущую кромку инструмента. При нажатии дважды запускается функция измерения, машина переходит в центр шпинделя, поднимается по оси Z, находит режущую кромку по высоте.
Далее машина переходит на измерения диаметра и мы приступаем к процедуре выставления на необходимый размер. Диаметр отверстия 18 с квалитетом H7, что означает необходимость попасть в допуск 18 мкм, поэтому при выставлении инструмента выбираем среднюю зону в данном допуске. Настройка в данной расточной системе по размеру завершена. Этот процесс занял гораздо меньше времени, и мы получили правильный результат.
Системы передачи данных
Помимо тех систем, которые передают результаты измерений, есть так же системы, которые позволяют загружать исходные данные об инструментальных наладках в базу данных, чтобы сравнивать номиналы и измеренные значения. Этот процесс является следующим шагом для многих предприятий в процессе автоматизации и в дальнейшем повышении производительности.
Большим плюсом является то, что могут быть подключены не только те новые системы, которые уже включают данные возможности, но и приборы Microset. На них тоже можно поставить данную модернизацию и использовать для дальнейшей интеграции с системой Tool Management. Так же огромный плюс этих систем – не только экономия времени и денег, но и исключение человеческого фактора — те случаи, когда оператор совершает настройку не так, как это было задано в технологии, могут привести к разным негативным последствиям. Однажды загруженные данные по инструментальной наладке будут измеряться автоматически, полностью минимизируя время и исключая человеческий фактор
В заключении хотим сказать, что те примеры улучшения эффективности производства, которые были представлены, показали нам, что цифровизация и диджитализация производства не такой сложный процесс, как может иногда казаться. Сокращение потерь и простоев оборудования, сокращение вспомогательного времени на подготовку инструмента в случае поломок — это первые задачи в построении процесса автоматизации. На выходе мы должны получить технологию, которая дает повторяемый результат и качественную продукцию, делает это быстро и эффективно, принося прибыль для развития и улучшения производства.
Важно, что автоматизация процесса не всегда является кардинальным решением, можно комбинировать старые станки и современное оборудование, в зависимости от целей и эффекта от данного вложения. Безопасность и стабильность технологии — это первая задача которую помогают решить данные процессы.
С уважением,
Сергей Валерьевич Показаньев
ООО Стилкам
Tел.: 8 (343) 382-52-03
Для оперативного решения вопросов можете также писать/звонить Сот/WhatsApp:
8 (922) 165 87 45
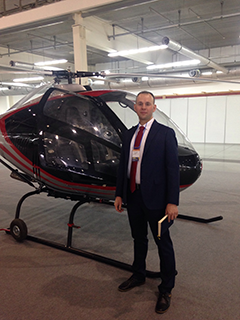

По вопросам функциональности оборудования, методики измерений, стоимости внедрения, вы можете связаться с нашими специалистами